What are the Effects of the Coating on the Valve Surface?
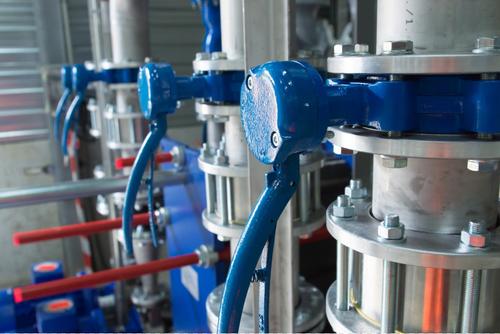
Generally speaking, cast iron and carbon steel valves are usually painted with different types and thicknesses of paint for good protection. Sanitary valves are generally used for the transportation of water, oil, steam, etc., and are in direct contact with the metal surface, thus prone to serious corrosion under the action of oxygen. Coatings are generally thought to protect metals from the following three effects.
Shielding effect
When a coating is applied to a metal surface, the metal surface is relatively isolated from the environment, so this protective effect can be called shielding. However, it must be pointed out that a thin layer of paint cannot play an absolute shielding role.
Polymers have certain permeability, and the average diameter of their structure pores is generally 0.000005cm-0.0000000cm, while the molecular diameter of water and oxygen is usually only a few angstroms, so they are free to pass through when the coating is very thin. Therefore, both the soft seal gate valve and the soft seal butterfly valve have strict requirements on the epoxy coating thickness of the surface.
In order to improve the impermeability of the coating, the film-forming material with small permeability and solid filler with large shielding should be chosen as the anticorrosive coating, and the number of coating layers should be increased to make the coating reach a certain thickness and compact without holes. For example, when the molecular chain of the polymer is less branched, more polar genes, and the cross-linking density of body structure is large, the air permeability is small.
A coating pinhole is formed in the process of coating, so it is closely related to the amount of solvent and volatile properties, the nature of the film-forming material, and construction conditions. After comparing the water permeability and air permeability of several coatings with different coating thicknesses, it can be seen that the anti-seepage ability of the coating is greatly improved when it increases to 0.3-0.4mm.
Corrosion inhibition
The internal components of the coating react with the metal to passivate the metal surface or create a protective material to enhance the protective effect of the coating on the specially required valve. Besides, the cast steel gate valve used in the pipeline can also act as an organic corrosion inhibitor under the action of some oil and drying action of metal soap.
Electrochemical protection
When the dielectric permeable coating touches the metal surface, it will form electrochemical corrosion under the film. The use of metal with a higher activity than iron, such as zinc, as the filler in coatings, can be sacrificial anode protection. In addition, the corrosion product of zinc is basic zinc chloride and zinc carbonate, which will fill the gap of the film, make the film compact, greatly reduce corrosion and extend the service life of the valve.